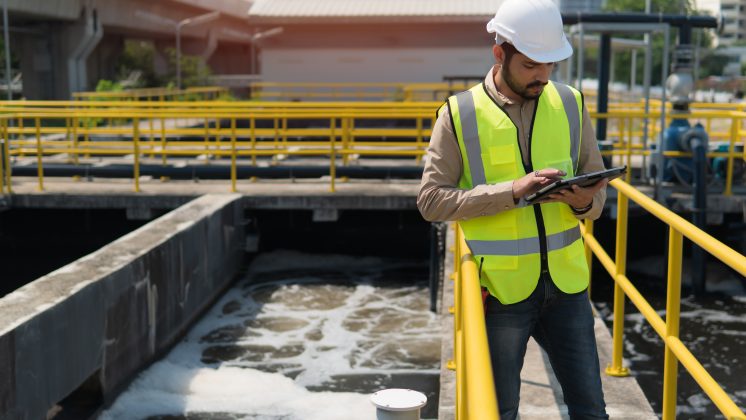
Transforming maintenance from a grudge purchase to a strategic investment
With South Africans enjoying a break from load shedding since March, one of my colleagues recently commented: “Maintenance is the reason our lights are now working.” Properly planned maintenance schedules across power-generating units are clearly contributing to Eskom’s current success rate. Despite the obvious link between maintenance and improved service or product delivery, I have noticed in industry that there is still a tendency to view maintenance as a ‘grudge purchase’ …

Introducing Pragma’s Enhanced Asset Management Assessment Framework: AMIP
Physical assets must be managed effectively for a business to grow and be competitive. Across industries, management teams must handle the complexities of asset management to drive efficiency, reliability, and long-term value. It’s a challenge to get it right, but it can be done with Pragma’s updated and enhanced Asset Management Improvement Planning (AMIP) framework. Read more …
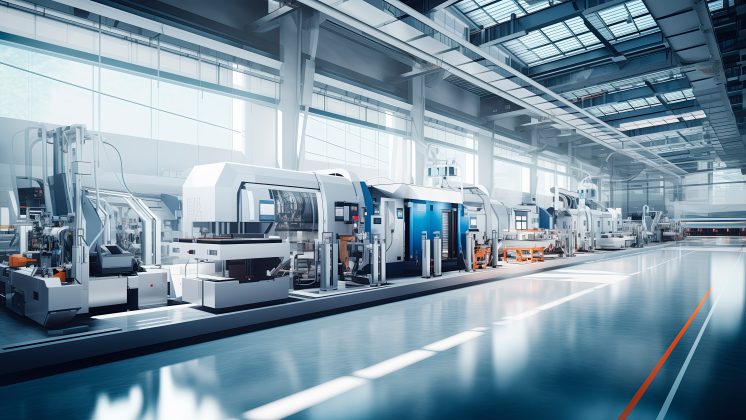
Enhancing OEM Service Revenue Growth: Overcoming After-Sales Challenges
Over the last decade, more and more Original Equipment Manufacturers (OEMs) have targeted after-sales services as a value-adding offering to complement their traditional focus on capital sales. Margins on capital equipment have been under pressure, and support from OEMs has become an important selection criterion in evaluating and acquiring new equipment. Read more …
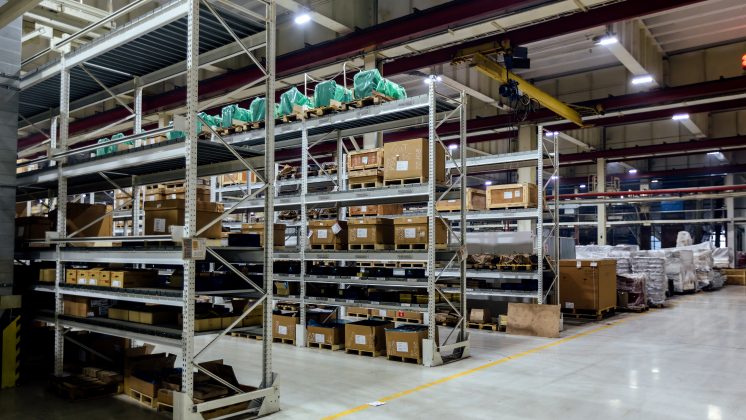
Are you proactively shaping your focused improvement process or is it evolving organically?
You might have an FI process that, in your opinion, is working just fine and is being improved as and when the need arises. But is it really good enough for your business? As a consultant specialising in FI I have often met clients who are satisfied with their improvement process, only for them to backtrack after being asked a few questions or seeing what ‘good’ actually looks like. Read more …