Wave after wave of load shedding has hit the country, as you would have experienced, no doubt. This has resulted in incidents where service providers and businesses in all industries have been unable to operate at full capacity. Initially, when all of this started in 2020, we ourselves suffered a generator failure at our head office, at a highly inconvenient time. These events prompted us to have a critical look and think about what should be in place to ensure a reliable backup when the inevitable will occur. After all, even backup plans need maintenance.
In this article, we offer some advice on how you can secure the reliability of your backup power. Further down we also introduce you to an Asset Health Management solution that we developed that has now been thoroughly tried and tested (thanks to the recurring power outages) and delivers real peace of mind.
Understanding your risk. What is the impact on your business when a specific critical asset fails?
Before you lift a finger or grab a meter, it is important to get a little (but good) understanding of the real-life situation. In any case where you want to ensure predictable, reliable operation of a thing (be it a machine, computer, or even a human) you should do a risk assessment to know:
- What are the critical functions you expect from the thing?
- What is the critical component that will affect this function?
- How likely is that component of the thing to fail?
In this case, the “thing” under discussion is a standby electrical power generator set, aka genset. For such a genset, the answers to these questions are quite simple and illustrated in the figure below.
Function | Components | Failure likelihood |
---|---|---|
Detect primary AC failure | Voltage sensor; actuated switch | Low |
Start the engine | Battery, starter motor, engine ignition, fuel | High |
Run engine for 2 hours | Engine, cooling, lubrication, fuel supply | Medium |
Generate electrical AC | Alternator, regulator | Low |
Switch supply connections | Transfer switch | Low |
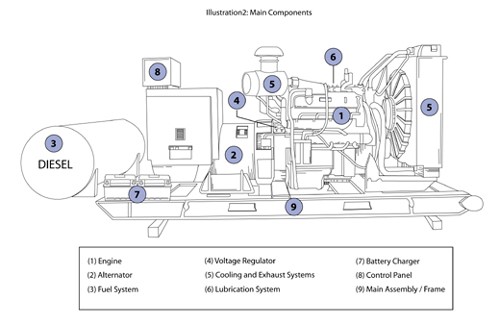
Maintenance best practices for a genset
To ensure good reliability and effective delivery of standby power from your diesel or petrol-powered genset, here are some useful simple tips to bear in mind when caring for such an asset:
- Ensure that all fluids in the machine are kept at the correct levels:
- Coolant level is between minimum and maximum on the level indicator
- Oil level is between minimum and maximum on dipstick or sight glass (do NOT overfill)
- The fuel level is between 75% and 100% of tank capacity. This reduces the possibility of condensation absorption into fuel, as well as the risk of premature depletion
- It is vital that the batteries, used to start the generator engine, are always fully charged. This is ideally confirmed by measuring the voltage of the disconnected battery to be > 12.6 VDC (for each 12V unit). Furthermore, battery electrolytes, for maintainable units, should always be at the correct levels in each cell of the battery set. For sealed maintenance free (SMF) units, the visual indicator should be (positive) green.
- Ensure that the AC mains power failure detection system as well as the automatic transfer switching (ATS) system is functional and is switched into the AUTO RUN or equivalent mode at all times.
- For gensets that switch on and transfer power automatically, and especially larger sets (100 KVA and more), it is essential to keep the engine oil and coolant at an elevated temperature, typically above 45°C. This ensures the immediate loading capability of the generator, without having to wait a few minutes for engine warm-up.
- Do regular visual inspection to ensure that all cooling system air ducts, inlet filters, radiators and extraction fans are clear of dust and debris. Air filter units should be regularly checked for blockages (check filter air block detectors where used).
- Do regular visual inspection for signs of fluid leaks or seepage. If any are found, ensure that rectification is promptly done, before leaks become excessive.
- Ensure adequate fuel reserves immediately available and fuel refilling is easily possible without spillage. Consider day tanks, hoses, filler fittings, transfer pumps, spare fuel drums, drum trolleys).
- During testing, ensure that when the engine is started up, it is not run longer than 10 minutes without load. If started up, it is preferable that the engine is run with a load, for a minimum of 30 minutes, observing temperatures, pressures, cooling and signs of fluid leaks. It is essential that a genset gets regular exercise.
- In the longer term:
- Simulate AC Mains failures at recommended intervals and ensure that the Mains/Generator/Mains switch-over cycles fully complete their functions.
- During simulated AC Mains failure tests, ensure that the engine starts immediately and smoothly takes up the load, while observing for signs of labouring due to possible overloading (excessive diesel smoke, under voltage, machine not achieving rated engine speed).
- It is a good practice to have the generator serviced annually, or every 200 operating hours, by a reputable competent specialist service provider.
- Plan and budget to pro-actively replace battery packs every two to three years, depending on the climatic conditions/exposure to high ambient temperatures.
- From a generator sizing and design point of view, ensure that the genset is not electrically overloaded during start-up and continuous running. Review the load configuration regularly to further ensure that load circuits have not crept up, and that phase balancing is maintained.
Lastly, but possibly the most important aspect to have assurance of asset reliability, is the disciplined adherence to your adopted maintenance and asset care programs. This often has to fend against operational and political pressure, but should never be compromised. Good mechanisms to support this, are clear service level agreements and computerised maintenance management systems.
Pragma’s Asset Health Management solution for commercial generators
After experiencing the effect of a generator failing when it should have rescued our operation during a power outage, we tasked a team to design and develop a maintenance solution that would give us 24/7 generator reliability and availability. This proved so effective that we packaged it and now offer an Asset Health Management solution on generators.
In a nutshell, the solution consists of a carefully selected technology stack to help monitor and predict potential failures, preventive maintenance plans and a set of reactive work management procedures. All of this is underpinned by digitalised workflow using work management applications and our On Key EAM system. A client’s EAM or CMMS can also be used. Furthermore, the monitoring solution is offered with a service option where our contractors will perform the planned maintenance or warning induced reactive work, or a client can opt to use their own staff to do this work.
We now enjoy an uninterrupted power supply and don’t have to worry about the dreaded load shedding schedule. So can you. Read more about the Asset Health Management solution here or speak to one of our Solutions Specialists to help you set up an affordable and reliable backup plan for power outages.