Authors | Carina van der Merwe and Andre Jordaan
“Optimise your spares”, they say, and to your credit, you immediately consider those spare parts that are just lying in the stores and have not moved for the last 5 to 10 years. Good start, but what about the rest of your inventory? What will the approach be for the vast majority of the spare parts your company holds? Do you employ a financial or logistics company? Or do you ask Pragma to use sound engineering and asset management principles to optimise the spare parts held in your stores?
This article aims to demonstrate the value of understanding the significant impact that engineering and asset management principles can have on spare parts demand forecasting. In model one, we proposed stock levels to cater for the unpredictable demand (breakdowns), not to the predictable (services, shuts, etc.). This can and should be used to motivate getting your work management process in order and maturing the environment to predictive rather than breakdown maintenance. Model two considered the impact of standardisation of equipment. The insights gained from these models demonstrated significant improvements in inventory optimisation.
Traditionally, the solution for spare parts optimisation has revolved around categorising parts and determining demand based on historical data or complex mathematical models. While this approach has its merits, it fails to fully grasp the underlying factors that drive spare parts demand.
Pragma’s interest in the subject of spare parts optimisation is threefold. Firstly, the opportunity presents itself during project execution as part of maintenance readiness. The reliability engineering function needs to specify stock levels for new equipment, and in the absence of historical data, a different approach is needed. Secondly, clients with poor quality consumption data also need to be serviced in the spare parts optimisation field and thirdly, it was necessary to improve our understanding of the impact that employing engineering and asset management principles could have on the optimisation of spare parts.
Demand forecasting can be approached by basing it on one of three forecasting principles:
- engineering expectations
- planned maintenance
- historical data
The value of planned maintenance in spare parts optimisation
Planned maintenance plays an important role in spare parts demand. It refers to the proactive and systematic maintenance, repair and replacement of equipment components before they fail.
Since it is proactive, one needs to question the reason for keeping these components as spare parts. Optimisation in this area means having stock levels that cater only for unpredicted demand such as breakdowns and excluding planned maintenance spare requirements from spare parts calculations. To this effect, Pragma has developed a model and generated spare parts data for three different scenarios.
The three models differentiated between high (R100 000) and low-cost (R500) versus fast and slow-moving spare parts based on the following criteria:
- Firstly, it considered, as a baseline, stock keeping when only keeping spare parts for breakdowns.
- Secondly, considering a relatively immature organisation with 67% breakdowns and 33% planned maintenance.
- Thirdly, there was a more mature organisation with 67% of spare parts demand coming from the planned environment.
The results looked promising.
For slow moving spare parts the savings are inconsistent. There was one spare and now you don’t have to keep one or there may have been two spare parts and now you only have to keep one or it still stands at two. Savings are, therefore very dependent on the cost of the specific spare in question.
Savings become more predictable with an increase in demand.
High cost, medium to high demand spare parts, can realise a saving of 10% compared to baseline when removing 33% of planned replacements from the demand for which you stock while it can be as high as a 19% saving when removing 67% of planned replacements from stock.
Low-cost, medium to high-demand spare parts can have savings in the range of 12 to 38%.
This approach requires a mature work management process emphasising predictive and preventive maintenance over reactive breakdown maintenance. By aligning with these principles, companies can maintain lean yet effective inventory levels, ensuring the availability of necessary components without excess stock.
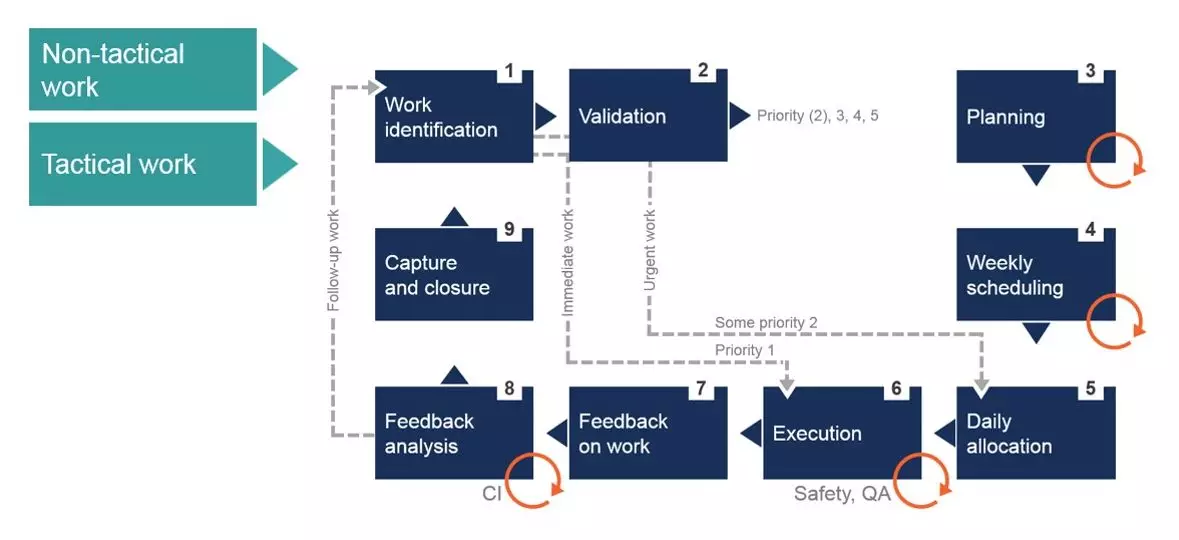
The power of standardisation in spare parts management
Standardisation of equipment is another key aspect that engineering principles can significantly impact. In many industrial settings, companies use various types of equipment from different manufacturers, leading to a wide range of spare parts in inventory.
During operational readiness, there are decisions that need to be made that are relevant to the standardisation of equipment and when considering replacement at the end of life, it is also prudent to consider the potential benefits that could be gained from standardising equipment. By adopting standardized components, companies can streamline inventory management and reduce the number of spare parts required. This leads to cost savings as standardised parts are often more readily available in the market, resulting in faster procurement and reduced lead times during emergencies.
The model generated for this case compared having six machines (or production lines) with the same spare parts versus having three machines with one type of spare and three with another type of spare. Once again the models differentiated between high (R100 000) and low-cost (R500) versus fast and slow moving spare parts. In this case a saving of between 27 and 39% was realisable.
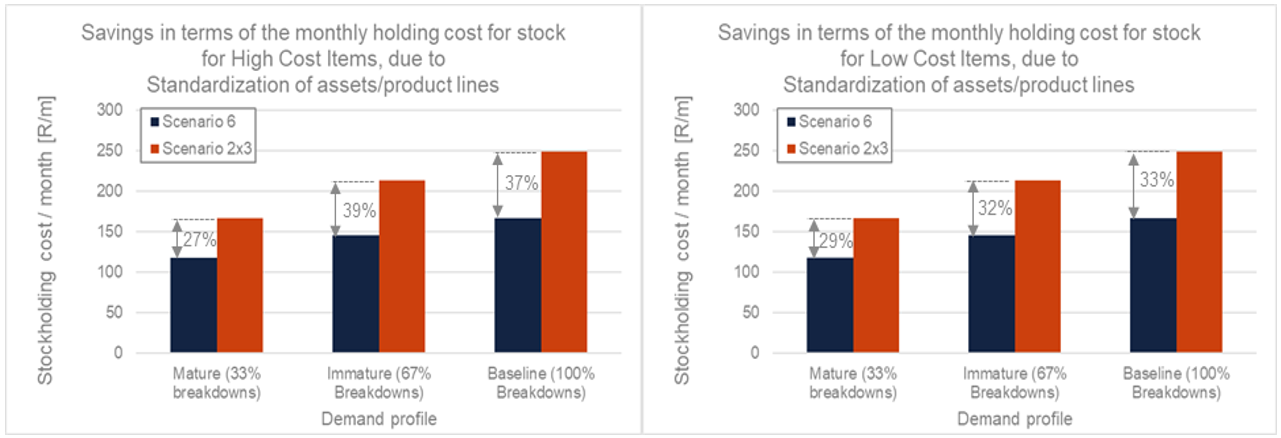
Conclusion
Optimising spare parts inventory requires a comprehensive approach that goes beyond addressing obsolete and non-moving stock. Integrating engineering and asset management principles into the optimisation process can lead to substantial cost savings of up to 38%, increased operational efficiency, and enhanced performance. By catering for planned demand through a mature work management process and standardising equipment, companies can achieve significant cost benefits of up to 33% and ensure a more sustainable and successful approach to spare parts optimisation. Embrace the power of engineering and asset management to unleash the true value of your spare parts inventory.