By Morné Steenkamp
Irrespective of your business or work environment, poor decision making often comes back to bite you. When talking about maintenance, it is something that could result in significant damage, costing the business dearly. How can we facilitate better decision making at ground level to prevent potential failures and save some money?
The solution depends on the operation and what is already in place to capitalise on. Thus, knowing your organisation well is imperative. Let’s start by creating some context.
In retail, branch managers are responsible for managing staff, stock management and, more importantly, the branch budget. The holy grail that will not be overspent. The majority of maintenance work gets outsourced. While specialised maintenance work like electrical or refrigeration is mission-critical and gets resolved reasonably quickly, general maintenance work (like leaking taps, broken door handles or loose tiles) often gets deferred due to the costs and perceived lower priority.
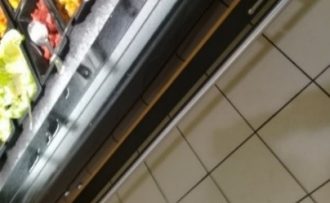
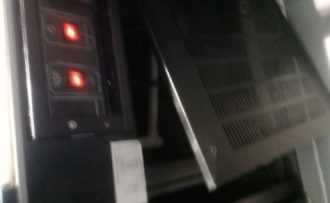
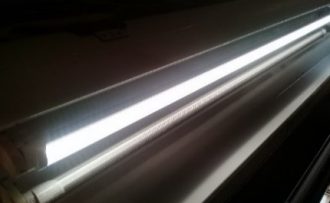
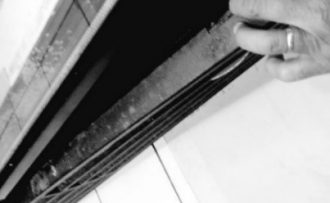
The fact remains that it is usually the “lower priority work” that comes back to bite by causing collateral damage if not taken care of resulting in higher repair cost and deterioration of the overall condition of assets. For instance, over time, a leaking tap in the staff kitchen could cause an entire Formica surface to warp and rot.
After analysing one of our retail client’s historical data our team found that the average cost of general maintenance work was R 2 608 per job with a labour component of 37%, material 47% and travel 16% (sample size of 4 750 general maintenance jobs). Overcharges for travelling of between 50% to 80% were not uncommon, especially within the boundaries of the metros (shorter distances) and material mark-up ranged from 25% to a couple of hundred percent.
While counter-intuitive for this type of environment, in-sourcing general maintenance stood out as an excellent solution. A central general maintenance team would be established who will visit each site once every couple of weeks. The fact that the company had other staff visiting sites on a routine basis for other operational reasons presented the potential of a “free ride” for this central maintenance team.
The four most essential elements ensuring the success of the project included:
- Eliminating unnecessary decision-making
Shift the decision of what site personnel should take, from “Should I have this work done?” to just “What work should get done during the next visit?”. A system where required general maintenance work can be logged, is also of great benefit as this will create structure and a central repository.
- Efficient software system
As mentioned already, an efficient call logging and work managed system is of great benefit. It allows site personnel to log required work as it is identified and put the maintenance team in a position to know what to expect and prepare before arriving at a site. The system should be efficient and capable of quick feedback on completed work to eliminate an unnecessary administrative burden.
- Cost-effectively
The three cost components of general maintenance work are labour, material and travel. By combining maintenance and operational travel, a saving of 16% on general maintenance was realised. While the material costs remain, the mark-up charges are saved.
- Standardisation
In most environments, maintenance tasks consist of a shortlist of recurring, everyday things that are generally in need of repair. Analyse and ensure you know that they are for your situation and ensure you have the required material for this work. As an example, condensers of self-contained fridges require cleaning quarterly. If this is applicable in your environment, ensure you have the necessary cleaning material handy. Below is a “before” and “after” picture taken of a condenser that was cleaned. Besides the improved condition, the cooling efficiency of the fridge will also improve, and the energy bill should reduce due to better thermal efficiencies.
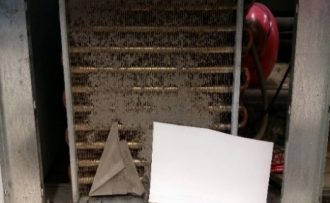
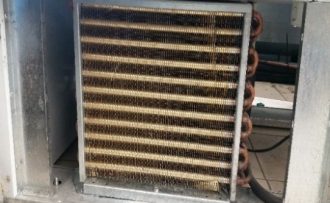
During this project, we found that a single general maintenance worker managed to complete 166 maintenance activities in a typical month. If you multiply that number of jobs with the average cost of R 2 608, the work performed amounts to the value of R 432 928 for only one month. That creates ample room to pay a salary, buy material and still have the potential to realise a significant saving.
Various components within general maintenance have the potential for cost reduction. It is well worth investigating what the potential is for harvesting some of these savings. In-sourcing is one of the possible options to be considered when you have a widely dispersed range of facilities like retail outlets. Apart from the monetary savings, the effort of dealing with the collateral damage caused by deferred maintenance works are also saved. Enabling this mind shift frees up branch managers time to focus on delivering more value at store level.