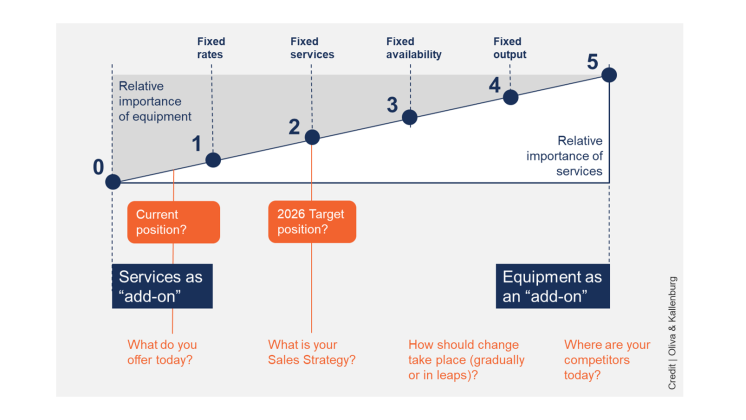
Servitisation
Servitisation refers to an Original Equipment Manufacturer’s (OEM’s) progression from an equipment-centric to a service-focused organisation, as shown in the equipment–service continuum diagram. As margins on capital equipment have been placed under pressure, OEMs’ service support has become a significant selection criterion for evaluating and acquiring new assets. Professionalising services have become essential for OEMs to sustain their capital sales and grow their overall sales revenue.
But where should the OEM position itself on this continuum? What is the competition doing, and what are clients’ expectations? Connect with us and let us assist you with this strategic servitisation topic.
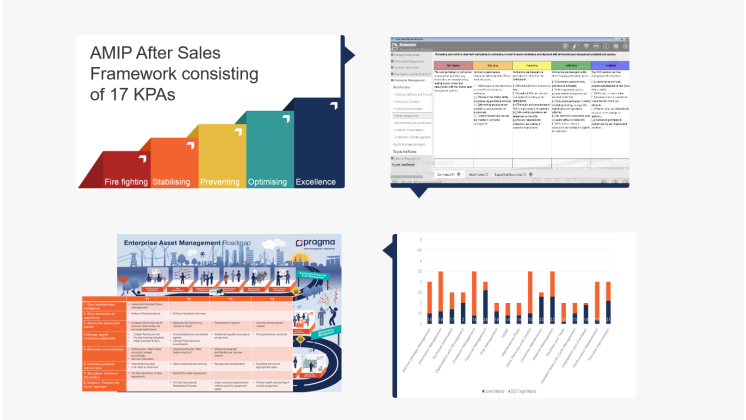
Developing an after-sales strategy or roadmap
With many OEMs operating in an equipment-centric environment for most of their existence, servitisation is painful and provides many challenges. Departments and processes originally streamlined to support equipment sales must be recalibrated to deliver a new product called ‘service’. This can be achieved if departments and roles work together towards a common goal, directed and guided by a clear strategy or roadmap.
The first step in developing such a strategy or roadmap is understanding your current maturity related to after-sales services. At Pragma, we work with an OEM to help establish a realistic current state picture and then develop a pragmatic roadmap to assist the OEM towards its chosen servitisation end-state.
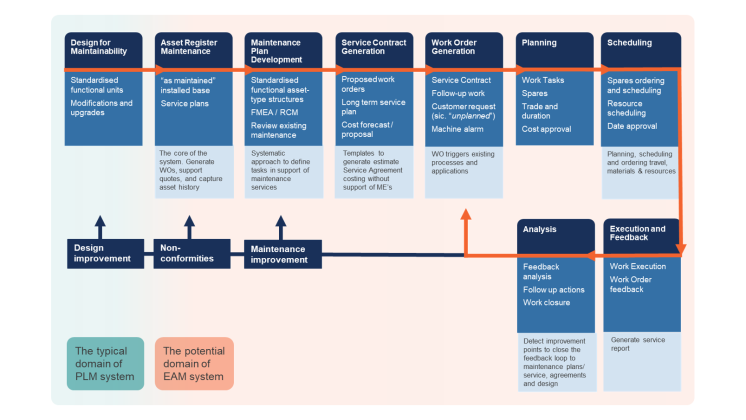
Selecting and implementing an EAM system to improve efficiency
OEMs have grown up with product lifecycle management (PLM) software tools to manage their design and manufacturing processes. However, although the name suggests that the PLM software manages the equipment from cradle to grave, it is, in most cases, only effective for controlling new equipment up to the point of leaving the factory door. The rest of the lifecycle is a separately recorded story, with most OEMs using a magnitude of systems, spreadsheets and custom applications to try and keep control of their installed base. Field Service applications are often purchased to manage the tail end of the process; ERPs are manipulated to support spare sales with Excel, filling many gaps.
But what does your organisation’s ideal system landscape look like, and how do you get to this picture? We help OEMs understand all the processes and supporting systems required to deliver their services efficiently and effectively. We assist them with a practical roadmap to do this in a controlled manner. Get Pragma’s After-Sales Service process here.
Streamlining after-sales services for OEMs
After-sales services are essential to keeping your client base happy and loyal. We help OEMs gain complete visibility across their installed base while managing service contracts. With our asset management service, field engineers and contractors deliver all service events. The On Key product suite plays a significant role in digitalising work processes to speed up turnaround time, eliminate human error, and complete sign-off and contractor invoicing.
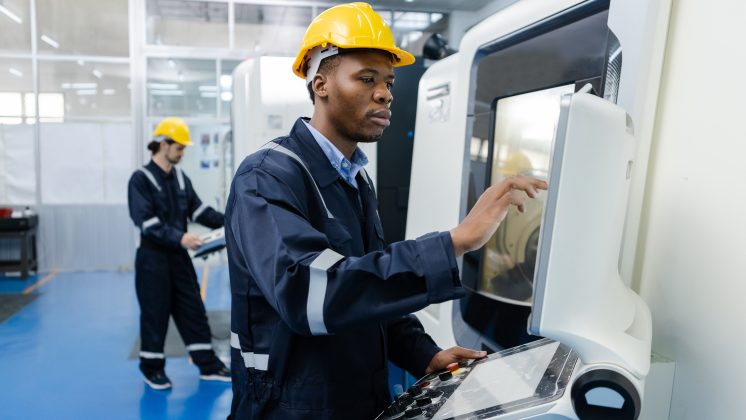
After-sales as a service. Performing any part of the after-sales process as an outsourced service.
The After-Sales business process must operate as effectively and efficiently as the OEM equipment. Business process outsourcing is valuable for assisting an OEM with its servitisation drive. Outsourcing the whole after-sales process, or selected activities to be performed by a specialist service provider, ensures the OEM can maintain its focus on designing and building the best equipment while gradually learning and mastering the service-focused characteristics. At Pragma, we perform many outsourced activities for OEMs through a value-adding service partnership.