On the evening of February 21, 2019, condition-monitoring specialist, Martec unveiled its new brand and outlined its future strategy. “Martec has embraced Industry 4.0 and is excited about the possibilities it offers for huge advances in plant reliability and infrastructure integrity, “said the Pragma company’s MD, Johannes Coetzee.
Opening the celebration of Martec’s new brand, Adriaan Scheeres, the CEO of the company’s parent, the Pragma Group, talked of a meeting earlier in the day with the COO of a large corporation, “We spoke about maintenance practices not being in place, equipment being pushed to its limit and deteriorating too fast, and funds being unavailable. It’s was all about ageing assets, ageing assets and more ageing assets,” he began.
“On the aeroplane, I read about company strategies which cannot live without new technology. Now it’s all about how Industry 4.0, IIoT, machine learning, virtual reality and all of these smart technologies should be incorporated in the future thinking of CEO’s strategies” Scheeres said.
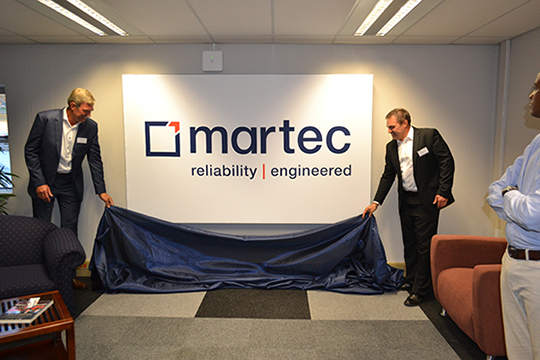
“I can proudly say that Pragma is continuously in the process of repositioning its services and researching new technologies to ensure that we can accommodate current issues such as those being experienced by industry while migrating towards future technologies.
“The wonderful thing about Industry 4.0 is that it is ideally suited to us in the asset management fraternity. It enables us to get to grips with what is going on in the ‘hearts and minds’ of assets in real time” he said.
Over the years, he said, Pragma has grown its business from a maintenance management and training business to a fully fletched enterprise asset management business, now including a facilities management offering: security, access control and the management of assets in buildings such as air conditioning systems, and the Condition Monitoring of assets.”
Scheeres compared Martec’s offering, acquired only two years ago, to an ECG monitoring a patient’s heartbeat. “Martec looks deep into the hearts and minds of machines to analyse the onset of failure and predict when it is likely to happen in the future – and predictability is something all engineers and plant operators love to have.
“We want to be able to predict exactly when an asset will fail and understand exactly why. That is why we added Martec to the Pragma Group and tonight is Martec’s time to say yes to this ‘marriage’,” he said.
Taking over the podium, Johannes Coetzee added to the ‘marriage’ analogy: “Having been in this relationship for two years, today we present our baby. We felt it was important to introduce a different logo to mark an exciting turning point in our condition monitoring offering. We are immensely proud of our logo and the repositioning of Martec’s brand. It symbolises a departure onto a condition monitoring platform at a new level,” he explained, before inviting Scheeres to help with the unveiling.
“Pragma brings a wealth of knowledge concerning enterprise asset management and an increasingly important subset of that knowledge involves condition monitoring. We see the integration of condition monitoring into the asset management world as offering the best of both worlds for plants and businesses.
“You will notice our strapline has been shortened to just two words: Reliability: Engineered. This reflects our belief in reliability as a complete entity in its own right, with a unique function within every business. Second, we implement reliability from an engineering perspective. Custom made solutions that are specifically engineered to client and plant needs are necessary, with asset reliability and plant integrity as key goals,” Coetzee explained.
Moving through to Martec’s technical area, he unveiled a summary slide outlining the expansion of the company’s offering. “We take pride in bringing the best condition monitoring solutions into the Southern African market and Mario Kuisis, my predecessor, was very good at tracking emerging trends.
“Many companies went directly into supplying vibration, oil analysis and thermography equipment, but Martec, from the word go, recognised that the electrical side of condition monitoring was the fastest moving. He was instrumental in entrenching our business, from a service and technology perspective, as the electrical condition-monitoring specialist.
“Today, we have 26 principles supplying us with state-of-the-art technologies, and we are at the front end of these concerning local expertise,” he noted.
Turning attention to his one-slide presentation, he says Martec’s raised platform is built on five key service offerings. “Our two trusted steeds remain Technology Systems and Field Services. These are the two pillars that have enabled us to build to where we are today. We bring in the best monitoring technologies, handheld devices, sensors and software tools into the market and we gather skilled people around each of these to ensure successful implementations,” Coetzee told us.
“Some of the foremost experts from the power industry work for us at Martec. When it comes to transformers and how to maintain them, switchgear, cable fault finding and monitoring for partial discharge, we have service experts at the highest technical levels,” he added.
Martec’s Training Academy is highlighted as a third well-established service. “We are engaged in a battle for skills. We don’t produce enough skilled people for the needs of plants. We strive to bring foremost global experts into the country to pass on the highest levels of understanding, and the Academy is not only about knowledge, it is about accrediting people with directly useful skills so that they can go back to there plants and add real value,” Coetzee assured, adding that a new ‘Essentials of condition monitoring’ course will be introduced very shortly.
Leveraging its access to Pragma’s experience, Martec has introduced a dedicated advisory service as its fourth offering: “to identify risks and put in place long-term strategies to minimise them”.
“How can we integrate our solutions into a complete programme that will drive plant reliability up, along with plant integrity and sustainability?” he asked. “This requires an understanding of the criticality of the plant and each piece of process equipment. We ask how this might change when critical units break down, and we do a plant-wide assessment to establish the optimum levels of monitoring and technology to minimise reliability risks and drive the bottom line,” he explained.
Fifth, he cites the Industry 4.0-related primary reason for the new brand. “This is the real level shift for Martec, which we call ‘In-time monitoring and diagnostics’.”
“The reality is, to make sure a plant is reliable 24/7, one cannot rely on individual people, no matter how skilled they are. Experienced people leave, taking their knowledge and experience with them.
“We see the pooling of data about a plant as an essential way of capturing knowledge for use long term. We want to take Industry 4.0 into real use, making plants more reliable, improving throughput and profitability. We strive to bring all of these together in a real way by monitoring, collecting, analysing and, most importantly, using the data to diagnose and track plant health without interrupting any part of the process – or even being near the plant,” he informed us.
But the ‘real’ approach is not free of skilled people. “By using the remote managing capacities of Industry 4.0 to manage many distributed assets around the country, we can afford to employ dedicated specialists for each equipment type,” he continued.
Using transformer monitoring as an example, he says that if a plant depends on one or two transformers, they cannot usually afford to have a dedicated specialist caring for them. “They don’t break every day”.
“But we have specialists in transformers that can be deployed to look after a collective set of transformer assets from many plants. This makes it economically viable for every critical transformer in our care to be monitored 24/7 by experts,” said Coetzee.
Pointing to his transformer team clustered around a screen running a simulation, he said: “Right here we are creating an actual partial discharge event and demonstrating how we can detect it remotely and respond. Over the years, Martec has saved many companies huge amounts of money by detecting the onset of partial discharge and responding in time. Industry 4.0 technology allows us to collect data via internet-connected sensors, load it to the cloud, analyse it and, through the help of specialists, predict when partial discharge is likely to occur – and respond in time,” he explained.
“A large percentage of failures can be prevented if we have in-time information – and we can already do this. This is the future,” he concluded.
This article first appeared in MechChem Africa on Friday, 1 March 2019. Author | Peter Middleton